It’s all in the details
With new, smart hanging solution, powder coating specialist Proton Finishing Alsab has achieved world-class energy efficiency. All thanks to its great cooperation with the local supplier HangOn.
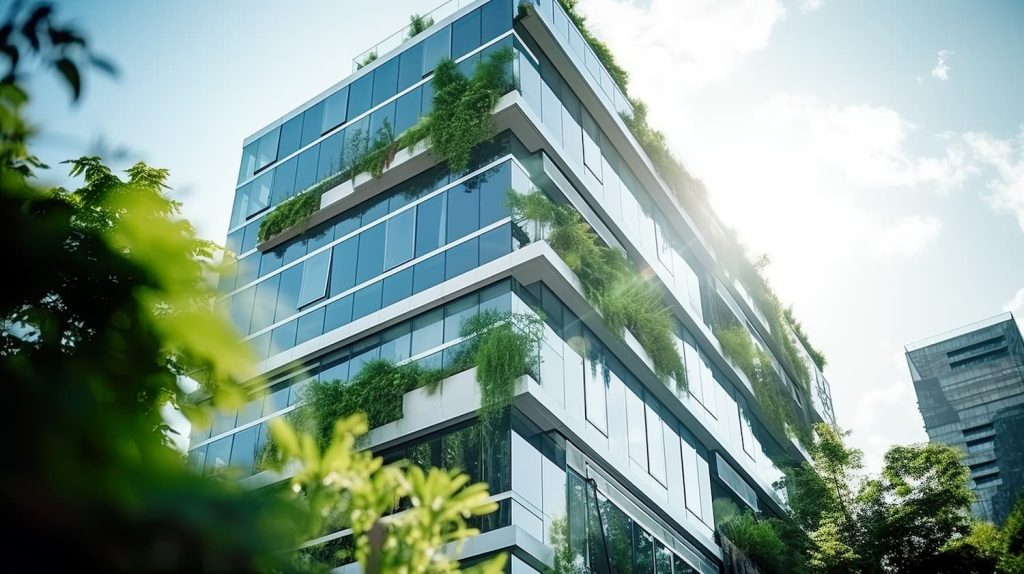
When the recent energy crisis hit, all of Proton Finishing’s units began to evaluate the potential for energysavings and further mitigation of their carbon footprint. This would prove to be a challenge at Finishing’s unit in Anderstorp.
“Our operations were already very energy efficient,” explains Liam Tran.
However, their years-long collaboration with HangOn gave them the idea to review the actual hanging process. Perhaps there was energy to be saved?
“We’ve developed our own spreadsheet programme called HangOn Coating Calculation, which takes into account the entire powder coating process – not just the hanging process. And it confirmed that there were great opportunities for streamlining,” says Jonas Törnquist.
Hard to keep up
Before painting, all parts are hung on a fixture, which then goes into the paint booth. At Proton Finishing, and almost all other powder coating companies, this job is done manually.
“Right now, there’s very little potential for automation in this industry, because we’re often dealing with big variations and short series. You have to reach very large volumes for automated hanging to be an option,” says Jonas.
At Proton Finishing Alsab, the painting line has a bottleneck that cannot be eliminated: there is simply a limited area in which the actual hanging can be done.
“We just can’t fit as many people in there as we want, which made it tough to keep up with the painting line. The number of parts that could be hung was also limited by ergonomics. You can hang things at face level, plus half a meter up and down. The rest of the hanging fixtures went into the paint booth empty,” Liam explains.
“With the new hanging solution, we can fit 500 parts per metre instead of the previous 50, because we can hang the parts more densely and use the full height of the paint booth.”
Liam TranProduction Leader & Processing, Proton Finishing ALSAB
Ten times the parts
The solution was HangOn’s new standardised hanging system, HQW D. In this particular case, it featured a customer-unique pitch and length that allowed them to get the most out of the painting facility. The fixtures, which are one metre long, are preassembled elsewhere in the factory and then connected together to form two-metre-long ‘curtains’.
They are stored on specially designed trolleys that are then driven out to the painting line, where parts can be hung on them quickly and easily.
The result?
“With the new hanging solution, we can fit 500 parts per metre instead of the previous 50, because we can hang the parts more densely and use the full height of the paint booth. The employees enjoy much better ergonomics and don’t have to feel stressed because they can’t keep up,” says Liam.
A whopping 90% in energy savings
With more parts going into the paint booth, the unit also makes better use of its energy, and the quality of the powder is even better,because it doesn’t need to be recycled as many times, says Jonas.
“Our conservative calculations show energy savings of 90 per cent. Proton Finishing Alsab has gone from an average of 0.11 kWh per painted part to 0.01 kWh. And we’re talking here about levels that were okay from the start. This is world-class.”
HangOn in Hillerstorp
The family-owned company HangOn in Hillerstorp works with solutions for hanging, masking and handling in industrial painting and is a long- standing partner of Proton Finishing Alsab. Together, HangOn’s Jonas Törnquist and Proton Finishing Alsab’s Liam Tran have taken the hanging solution from good to world-class.
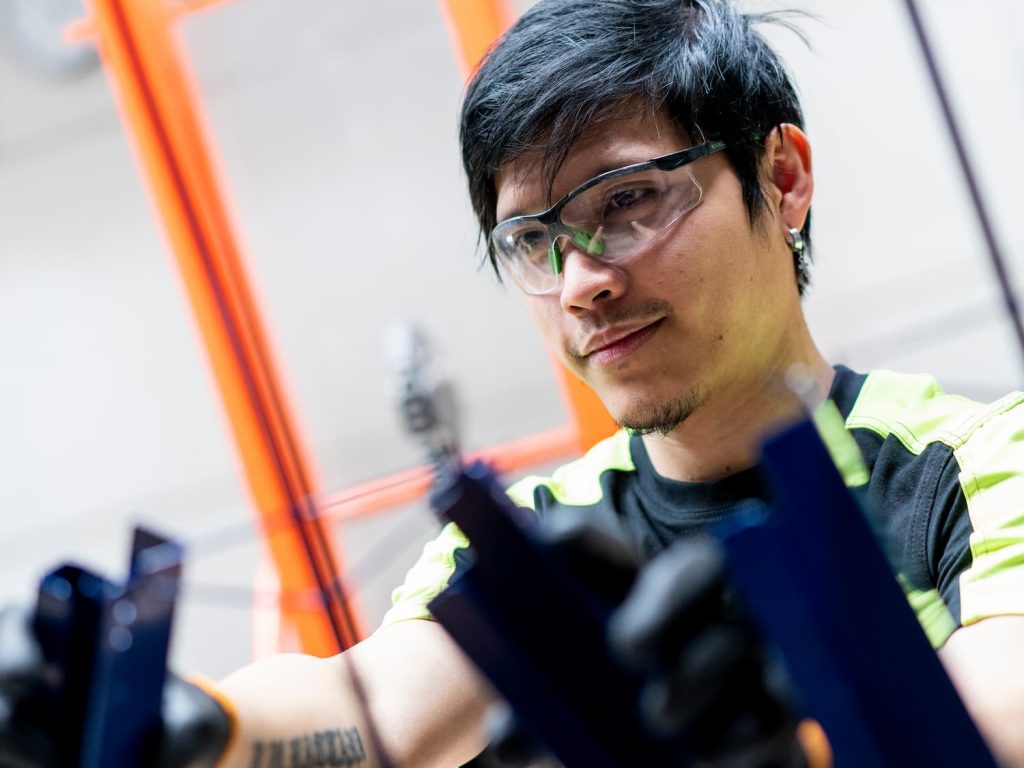
Want to know more?
Welcome to contact us to ask your questions and discuss which surface treatment meets your requirements and preferences.