Alkaline zinc
Alkaline zinc is a coating with broad horizons. It is an electrolytic, inorganic, corrosion-protecting coating suitable for most steel products used in semi-corrosive environments/applications. With this type of galvanising you save costs and also get a foundation suitable for varnishing.
Our plants that offer this process:
- Anderstorp Grand Prix – Hanging application.
- Hillerstorp – Hanging and drum application.
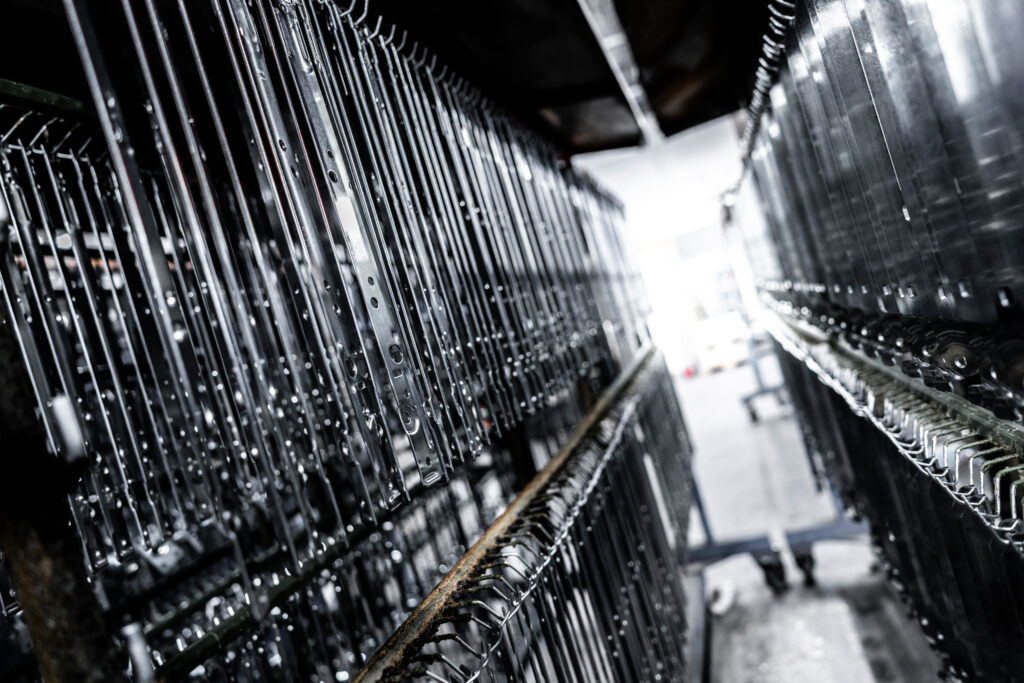
Why Alkaline zinc?
The thickness of the zinc layer can be adapted to customer requirements, but has good corrosion-protecting qualities even with thin layers. Most common is 8–12 μm.
Adding a sealer/topcoate will increase corrosion protection and give controlled friction when needed.
As this coating extends the lifespan of your product, it contributes to a more sustainable life cycle.
It has good metal distribution over the current density areas, which gives even layers.
The application temperature range is <+150°C.
Which products are suitable for Alkaline zinc?
- Screw joints
- Construction and window fittings
- Fasteners of various kinds
- Brackets
- Automotive products
- Pipes
Which requirements does Alkaline zinc comply with?
- Meets Volvo STD 121-0004 Y2000-3, 121-0006 Y400-3 and 121-0015 Y1500-3.
- Meets Scania STD 4111-C2-IF.
- Complies with the ELV and RoHS directives.
Corrosion performance with sealer as follows:
Passivation – Performance
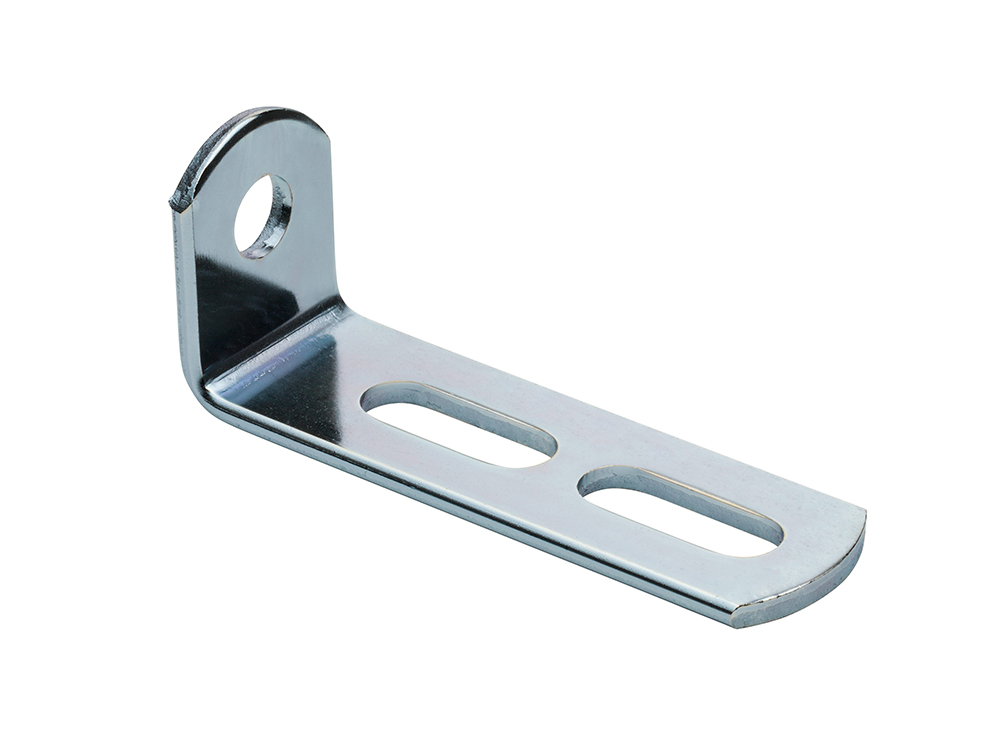
Satin to lustrous
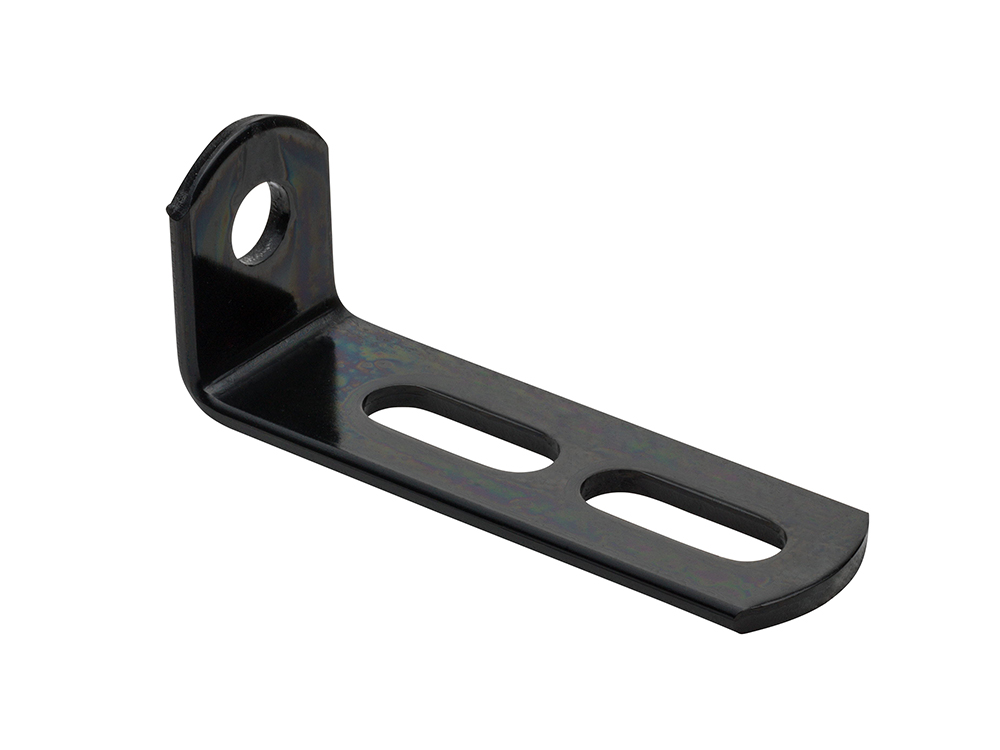
P4 black passivation (combined with sealer)
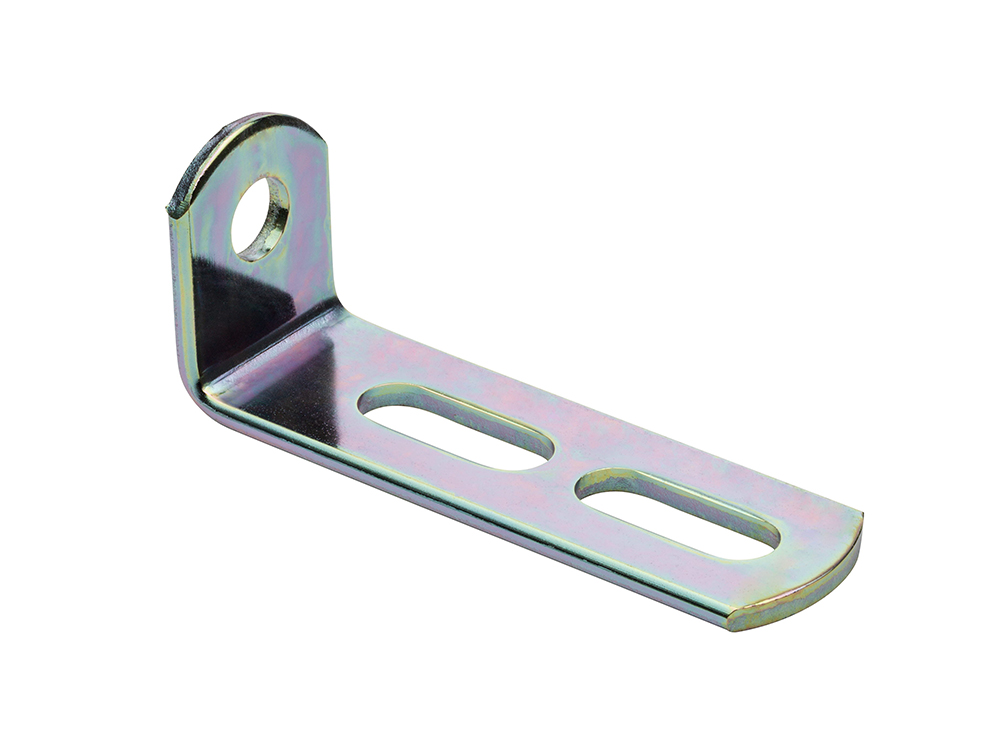
P5 iridescent passivation, drum application
Want to know more?
Welcome to contact us to ask your questions and discuss which surface treatment meets your requirements and preferences.